熱で成形できる木材、韓国から世界へ、
素材の常識を変えていく
熱で成形できる木材、韓国から世界へ、
素材の常識を変えていく
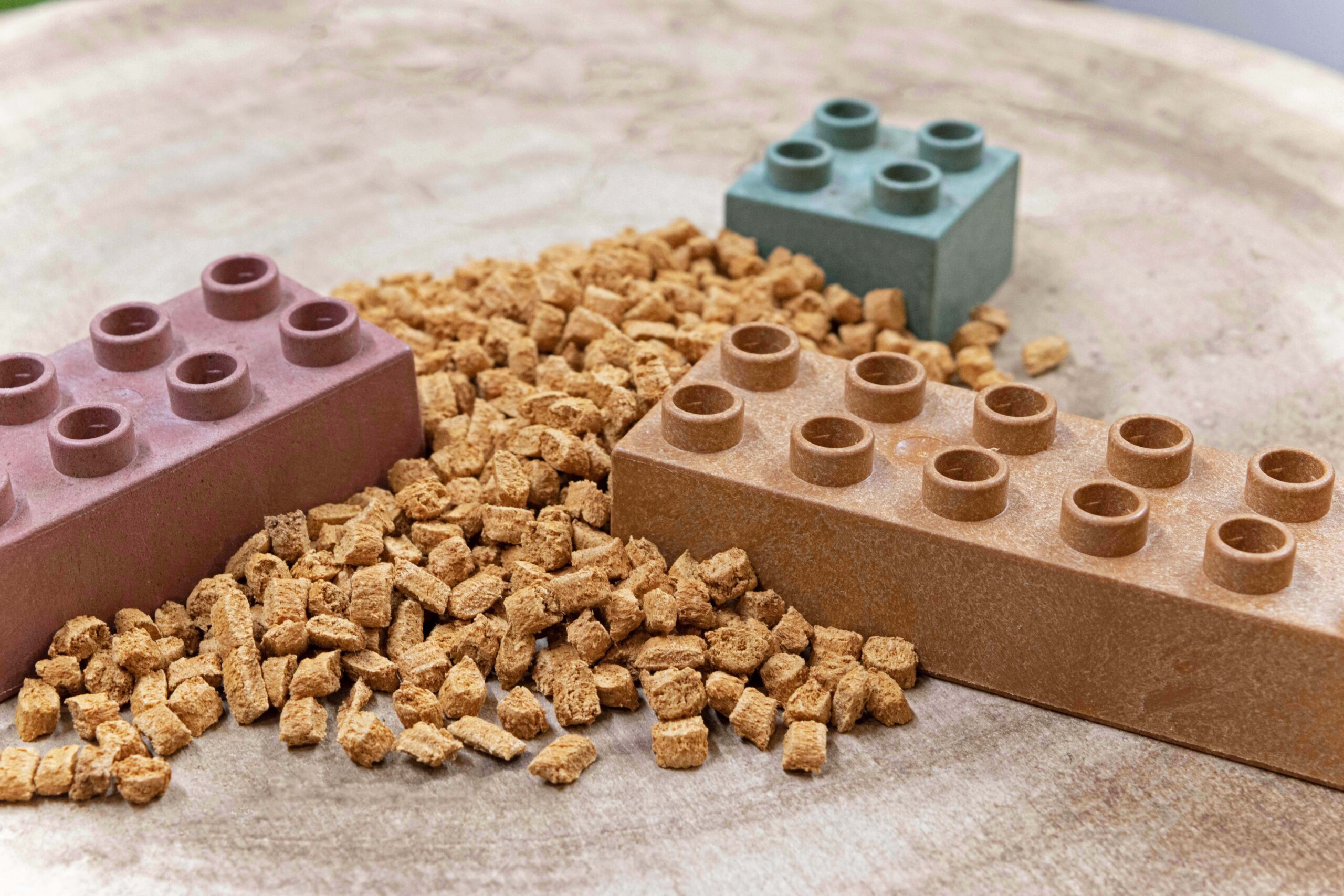
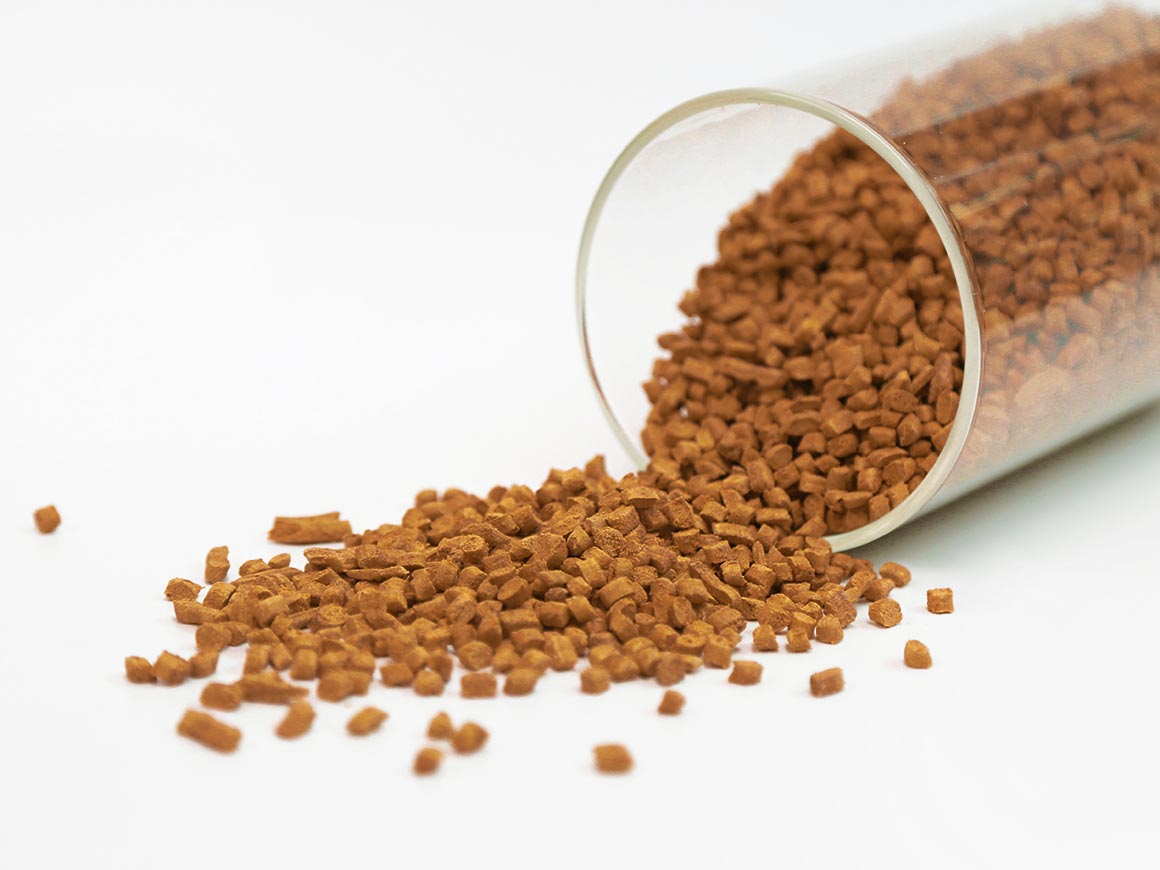
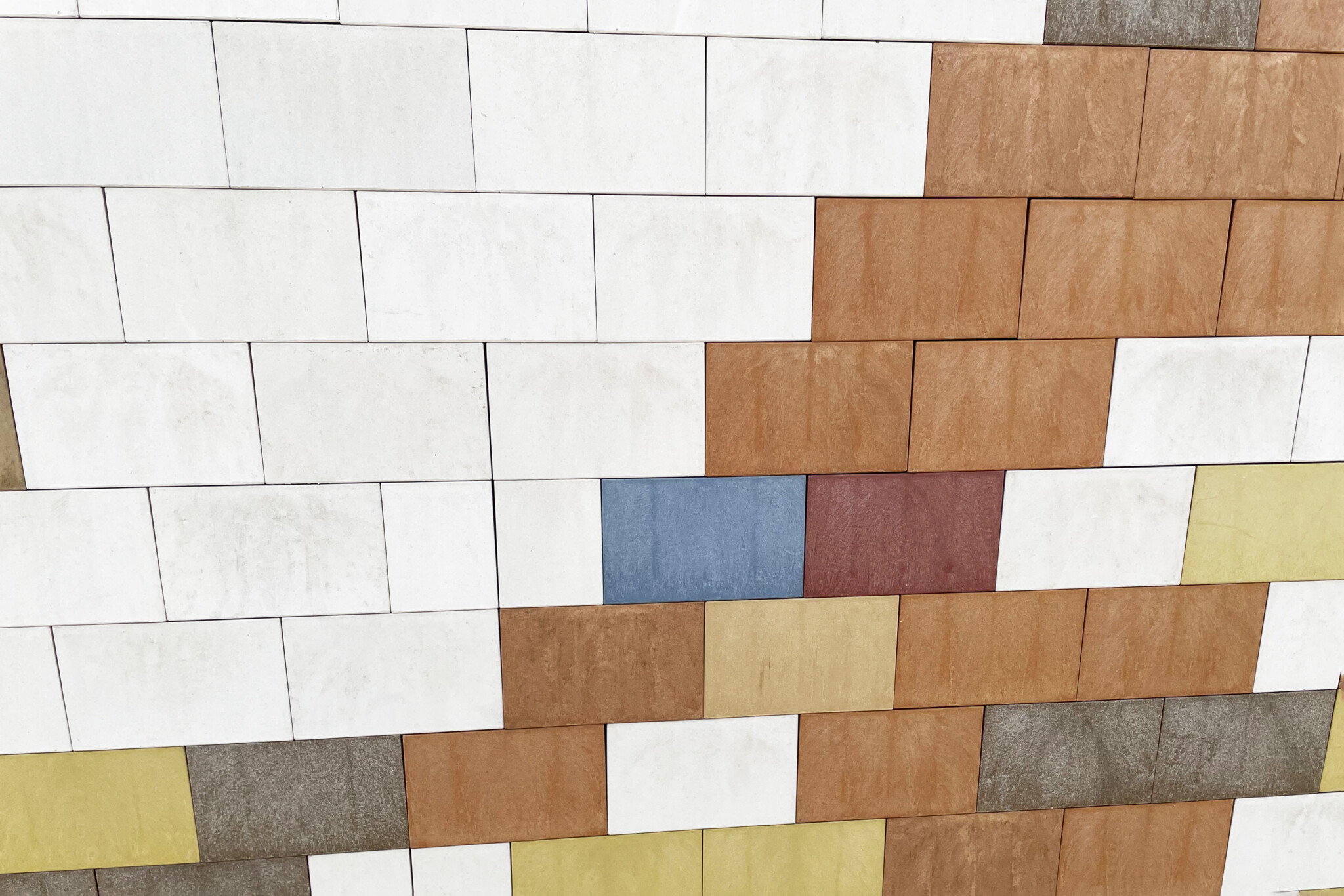
「成形できる木材」と聞いて、イメージがつく人は少ないと思います。
熱可塑性で、プラスチックのように金型成形が可能でありながら、木材としての認証を受けている。
これまでの常識を覆すような素材「CXP」を開発し、世の中に提案しているのが、韓国にある株式会社Dongnam Realize(ドンナム社)です。
CXPは成分の約70%が木材。間伐材やおがくずなど、廃棄されるはずだった韓国内の林業副産物を活用しています。
石油由来の成分が一切含まれていないにもかかわらず、従来のプラスチックと同様の機械で射出成型などが可能です。
脱炭素化の流れのなかで、プラスチックの代替となりうる新しい素材。開発部長のLeeさんに話を聞きました。
高い木材使用率と強度を両立した新素材「CXP」
2018年創立のドンナム社。開発を進めていた前身のPa-Dong(パ・ドン)社から、CXPのビジネス展開に特化する会社として設立された。
開発部長のLeeさんは、ドンナム社で働く以前も、環境に配慮した素材の研究開発に関わってきた方。
「既存の素材の欠点を補うような、より良い素材を生み出すことができるのではと思い、CXPの開発に加わることにしました」
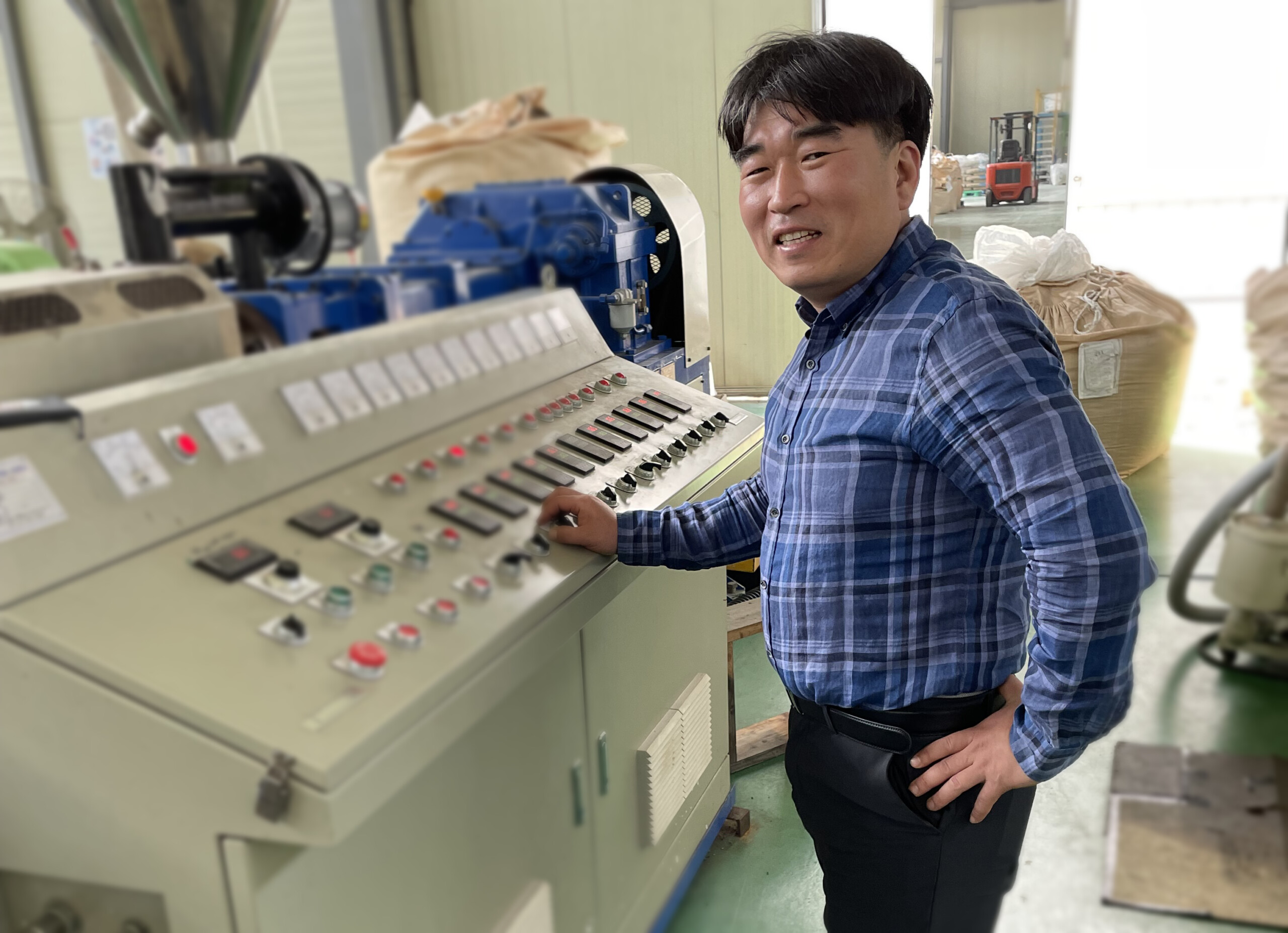
たとえば既存の素材でWPCというものがある。これは木粉とプラスチック樹脂を混合したもので、木材の使用率は標準グレードで全体の50%ほど。木材の割合を増やすことはできるものの、それに伴い強度が低下してしまう。
一方のCXPは、標準グレードの「CXP-SD」でも、70%が木材でできている。
木材のほかに含まれるのは、色と流動性を向上させる天然ミネラル顔料が10%、木材に成型性をもたせるプロポリスに近い成分が20%。石油由来の成分は一切含まれていない。
「物理的に接着しているのではなく、物質を化学的に結合させているのがCXPです。そのため、木材成分が多いにもかかわらず、強度などの物性が変わらない。すごく魅力を感じました」
CXPはヨーロッパ基準の国際森林認証PEFCで、木材として正式に認定。「成形できる木材」として、世の中にリリースされた。
前例のない素材。理解を広げるむずかしさ
「最初は、CXPはバイオプラスチックと同様に見られていて、世の中からの理解を得ることに苦労しました」
優れた素材ではあるものの、前例がなく、また価格も高いことから、すぐに取り入れてもらうことはむずかしかった。
そこで、2020年から「炭素倉庫」という生活雑貨のブランドを展開。身近に取り入れやすい商品を製造販売することで、世の中でCXPの認知度を上げることから取り組んでいった。
今では、炭素倉庫の商品は昨年対比5倍以上の売り上げに。
ペレット材料を購入し、自社製品に使用するメーカーも増加。雑貨のほか、工場で使用する大型パレットなどに、プラスチックに代わって取り入れる動きが出ている。
「現在、韓国国内で製造しているCXPは、月に150トンほどです。将来的にどんどん生産量を増やし、従来のプラスチックと同等の価格にすることも目指しています」
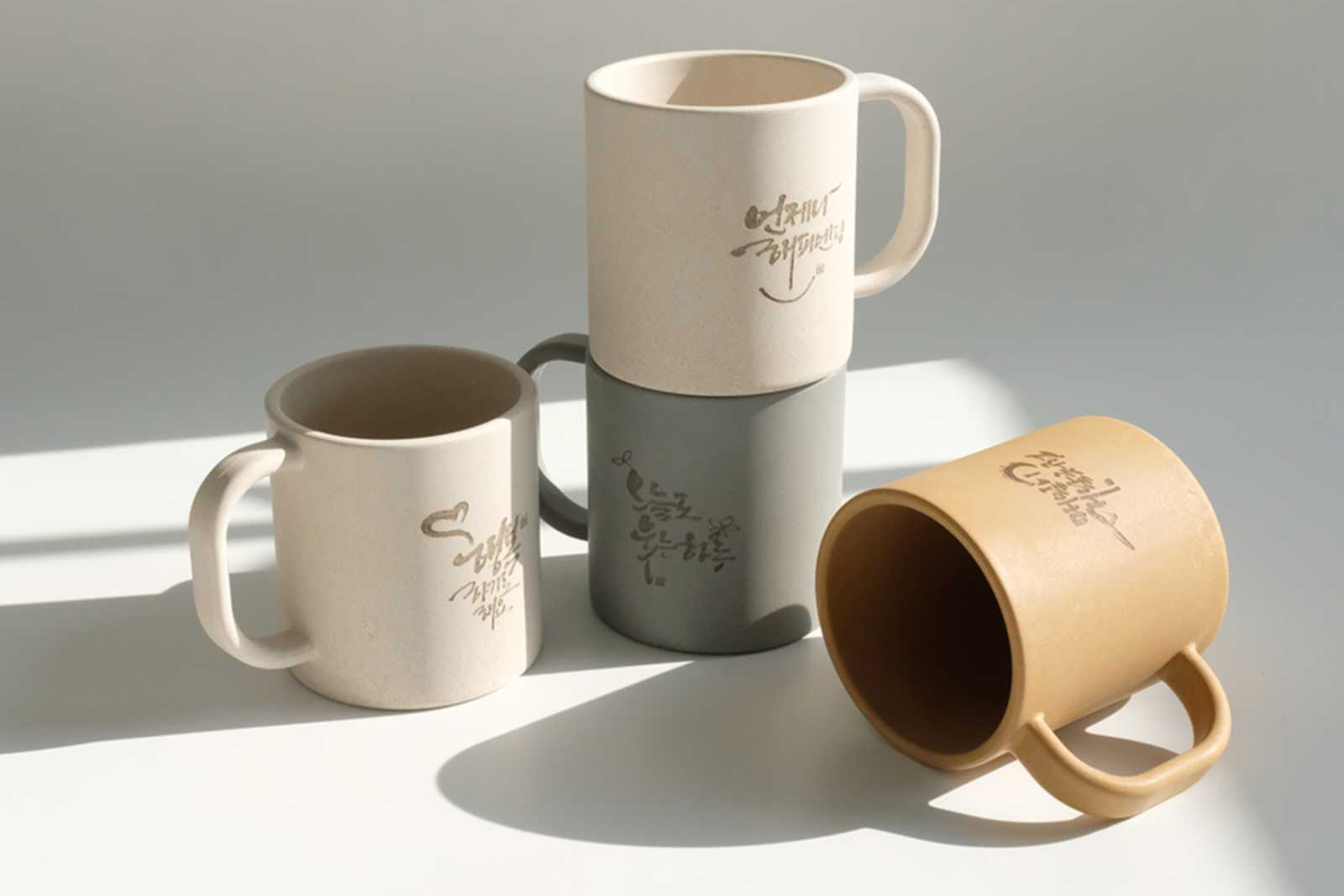
オプションとして、難燃、高強度、抗菌などの機能も付与できるCXP。
各添加剤も、プラスチックに使用する一般的なものではなく、木材由来の独自開発したものを使用。グレードにより、木材配合率は最低65%、最高80%になる。
クライアントの用途によって、カスタマイズも可能とのこと。
「現在プラスチック樹脂を活用しているメーカーで、CXPに興味があるならば、まず試してみてほしいです。まずはCXPの特徴を理解したうえで、取り入れてもらえたらありがたいですね」
二酸化炭素の貯蔵庫として、炭素ゼロに寄与する
日本同様、韓国も森が多く、国土の70%が山林地域。
大量に生まれる間伐材など、廃棄される木材原料を集めて、CXPのペレットはつくられている。CXPのために木が伐採されることはないという。
「木は、伐採後にそのまま自然環境に放置されると徐々に腐敗が進んでいきます。その過程で、木材の中に含まれる二酸化炭素が空気中に排出されていってしまう」
「CXPは数十年経っても腐るものではありません。木材が持つ二酸化炭素を内包したまま、CXPの形になる。製品自体が二酸化炭素の貯蔵庫になるんです。さまざまな炭素排出問題があるなかで、新しいかたちで炭素ゼロに寄与することが可能な素材です」
本来空気中に排出されていた二酸化炭素を、商品の中に閉じ込める。これまでの常識から考えると斬新さも感じるものの、合理的な排出削減方法でもある。
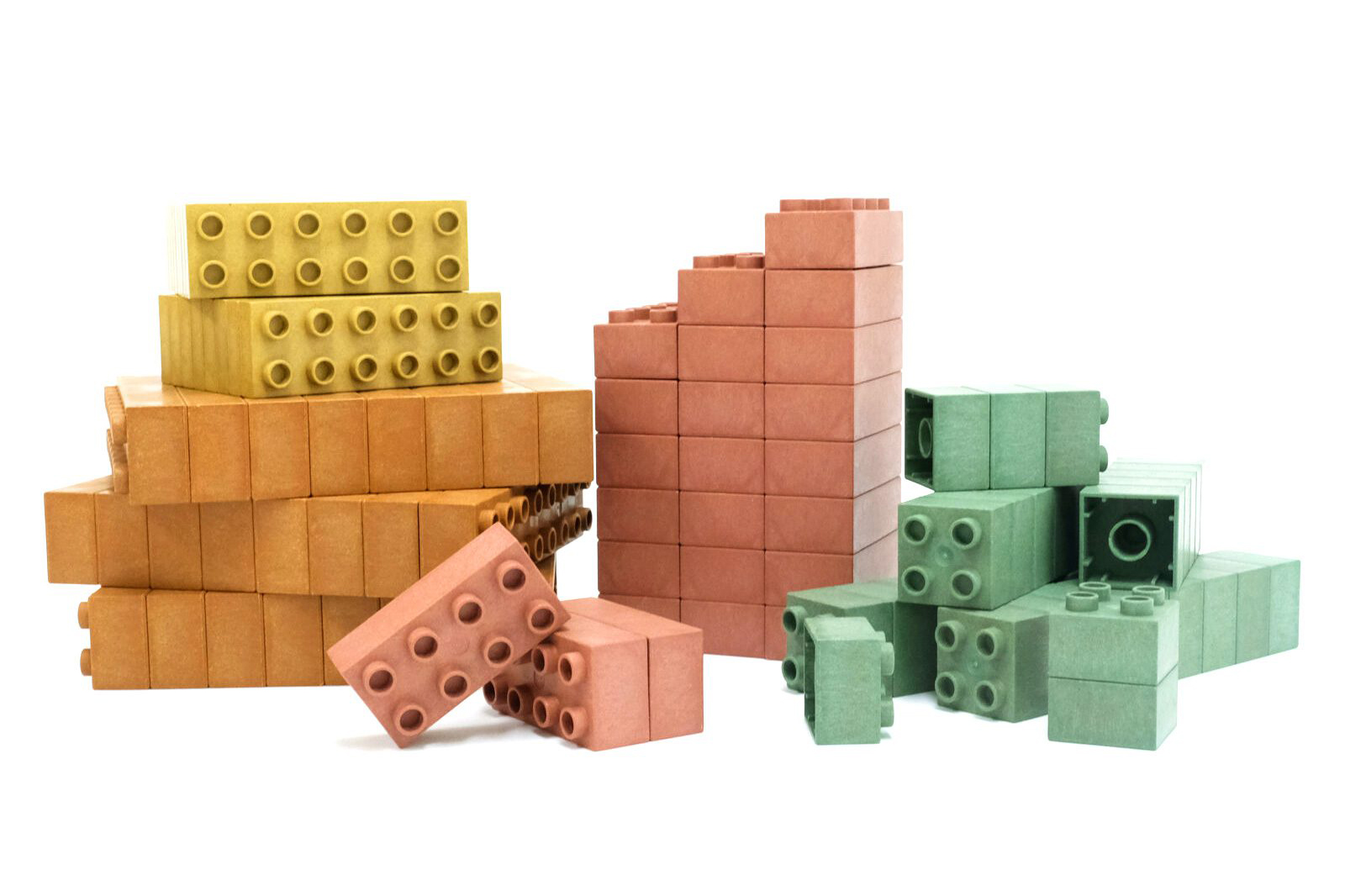
「不要になった場合はそのまま粉砕して、70%のリサイクル品と30%の新品を合わせることで、リサイクル可能です。熱可塑性なので、何回も繰り返し利用できます」
通常は複数の樹種が混ざっているけれど、たとえば使用する樹種をひとつに絞ることで、その木の物性がそのまま反映されたCXPを製造することができる。
「ヒノキに絞ってCXPを製造するテストをしたときは、完成品からヒノキの物性や香りが確認できました。値段は高くなってしまうのですが、よりCXPの認知が広まれば、プレミアムグレードで製造する可能性もあります」
建材の代わりにCXPを使用することで、二酸化炭素の排出量削減や、森の循環を促す。そんな未来が訪れるかもしれない。
プラスチックの代替品になるために
環境により配慮した素材として、石油由来のプラスチックの代替となることを目指しているCXP。
プラスチックと比較したときのデメリットは、透明グレードに対応できないこと。そして、木材自体が伸びない物性のため、CXPの成形時の伸び率にも限界があること。
また意匠面では、優しい色味や手触りが特徴の一方で、色鮮やかさや光沢のある質感を表現することはむずかしい。
どれも木材だと考えれば当たり前のことだけれど、プラスチックの代替を目指すのであれば、妥協したくないことでもある。
「透明にすることは不可能なので、現状のプラスチックを100%代替するのはむずかしいと思います。でも、できる限りの範囲で代替できるようにしたい。今はより伸び率が高いグレードを開発しています」
現在対応可能な射出成形や押出成形に加え、今後は真空成形やブロー成形にも対応できるようになる見込み。どれも通常のプラスチック樹脂向けの機械でつくることが可能だそう。対応できる加工方法が増えれば、製品の幅はおのずと広がり、CXPの普及につながっていく。
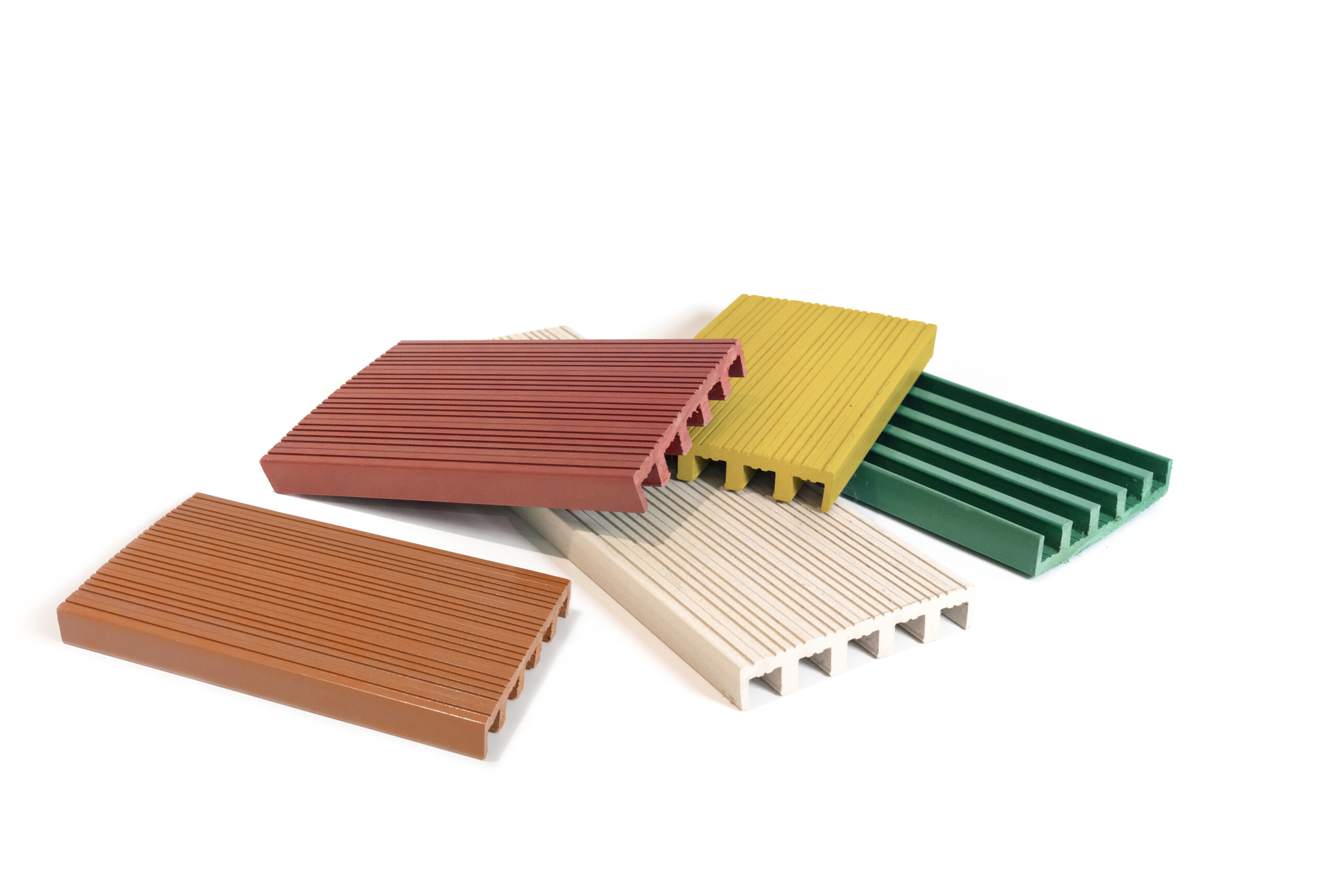
世界中でCXPの地産地消を目指したい
「あらゆる環境配慮型の素材が出ているなかで、『CXPがもっとも炭素ゼロに寄与する素材』だと、グローバルに認識してもらいたい。CXPが普及すればするほど、二酸化炭素の削減につながっていきます」
製造工程も、プラスチック樹脂よりシンプルだというCXP。製造による二酸化炭素排出量も少ない。
需要さえあれば、製造プラントを国外に設けることも十分可能だそう。
「今の韓国と同等の需要が生まれれば、日本にプラントをつくることができる。そうすれば、日本の間伐材を使用して、CXPの地産地消が可能になります。そのほうが、もちろん安価に販売もできる。まだ時間はかかるとは思いますが、さまざまな国でCXPを現地生産することも、将来的な目標に掲げています」

まったく新しい素材でありながら、魅力的な要素の多いCXP。
すべてのプラスチックの代替になることはむずかしいけれど、その一部でもCXPが利用され、世の中に認知されていくことは、つくり手と使い手の環境への意識を変えることにもつながっていくはずです。
当たり前にCXPが普及する未来に向けて、日々挑戦が続いています。